Högert BlauPower brushless motors
With our BlauPower brushless motor, Högert battery-operated power tools achieve the power and efficiency characteristic for corded power tools, they provide maximum resistance to high load at work, high velocity and durability of many years.
Högert BlauPower brushless motors mean:
- ultramodern design,
- four times as much power generating material as in traditional solutions,
- rare earth elements used to build efficient magnets,
- higher copper content in coils than in the case of competing devices.
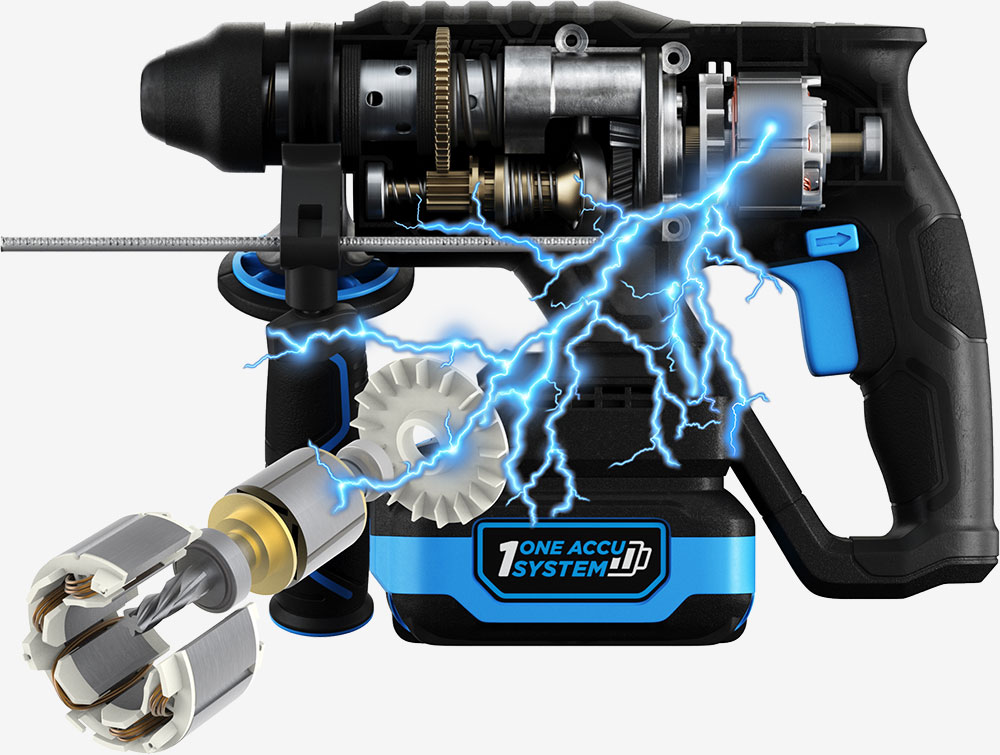
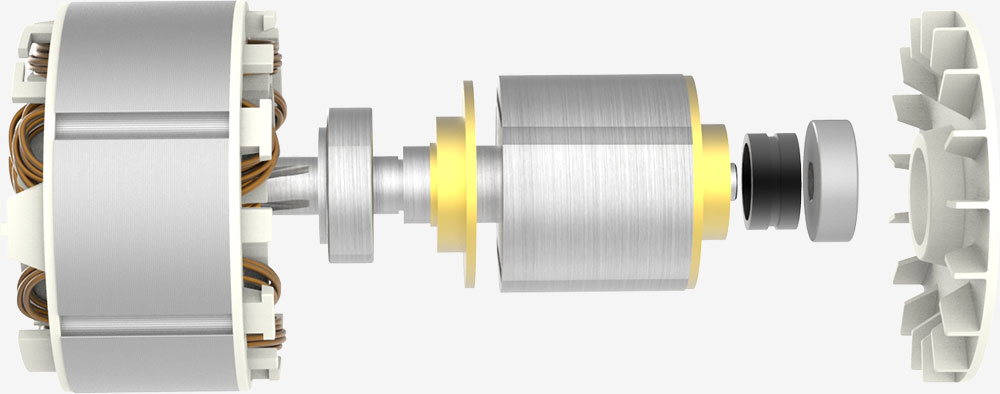
With these features, our motors are:
- stronger,
- faster,
- more resistant to loads,
- more durable,
- more silent,
- lighter,
- smaller.
Traditional motors
Traditional motors with brushes use a mechanical commutator and carbon brushes which generate friction, heat and scintillation when in contact with a rotor. Those elements are key to transformation of the battery’s electric energy to mechanical energy. That’s why motors with brushes usually achieve efficiency of about 65%. Further, their design makes the devices bigger and heavier. Friction leads to mechanical wear, negatively affecting the motor’s operational efficiency and durability.
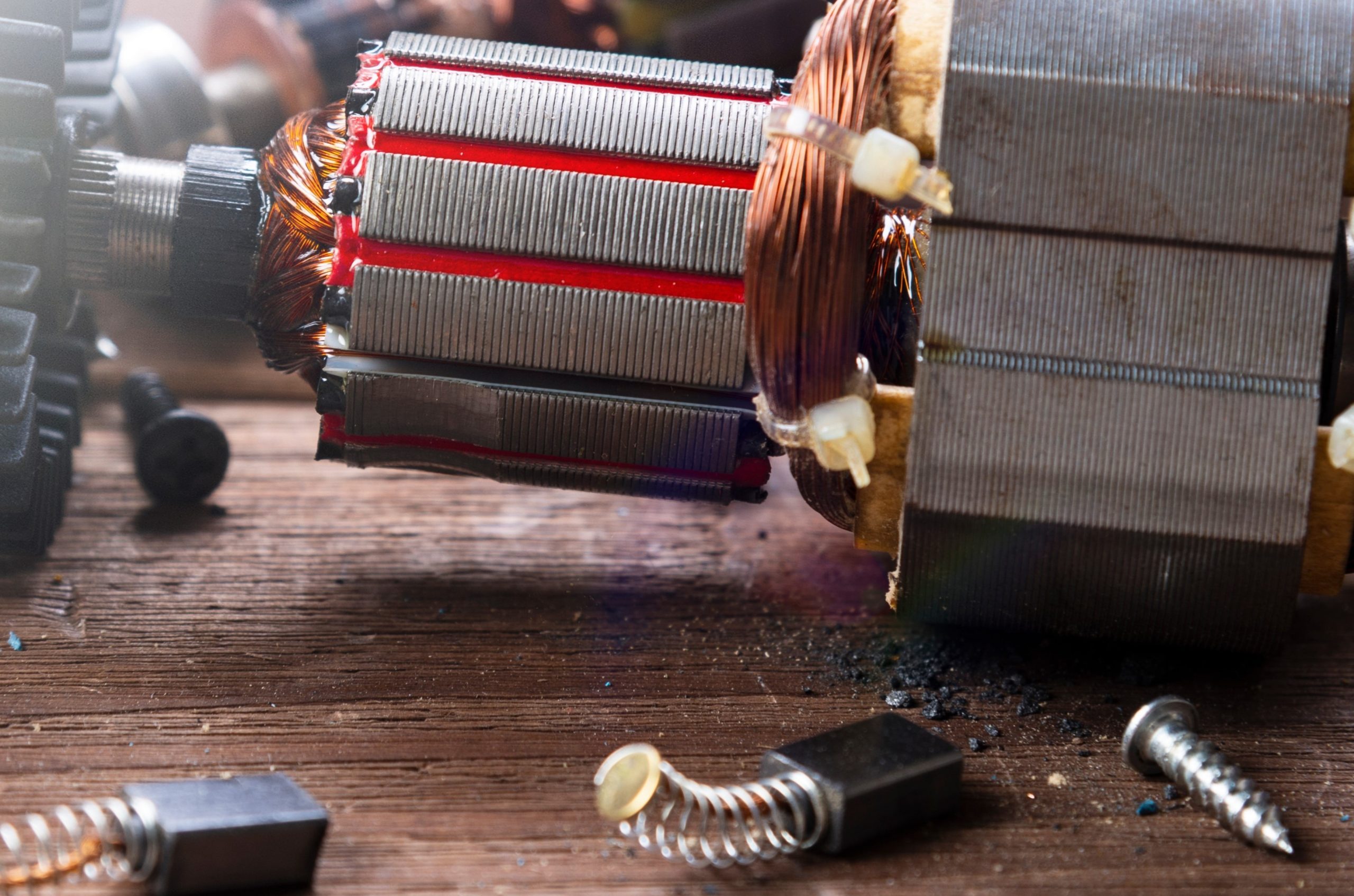
Operation of a traditional motor involves the brushes’ providing electricity through a constantly rotating commutator to coils on the rotor placed within a fixed-field magnet. Electricity generates magnetic fields in coils, causing rotation of the coil set, because each coil is pushed away from the similar pole and drawn to the opposite pole of the fixed field. To maintain the rotor’s rotation, the current must be constantly reversed – so that the coils’ polarisation keeps changing. Reversal of the current going through the coils causes the commutator to rotate.
Brushless motors
As indicated by their name, the design of those devices does not include brushes, which generates multiple advantages. By eliminating application of mechanical carbon brushes and replacing the commutator with electronic steering, the design is simplified and mechanical interaction between elements of the motor is eliminated. This results in a lack of friction, a cause of heat, sparks, sounds and mechanical wear. Thus, the motor becomes more effective energetically, more silent and more resilient to breakdowns. It doesn’t need replacement of used parts so often. A brushless fixed-current motor usually achieves efficiency of about 85%. Further, the easier design, eliminating heavy parts, affects smaller dimensions and lower weight of the motor, and consequently of the power tool.
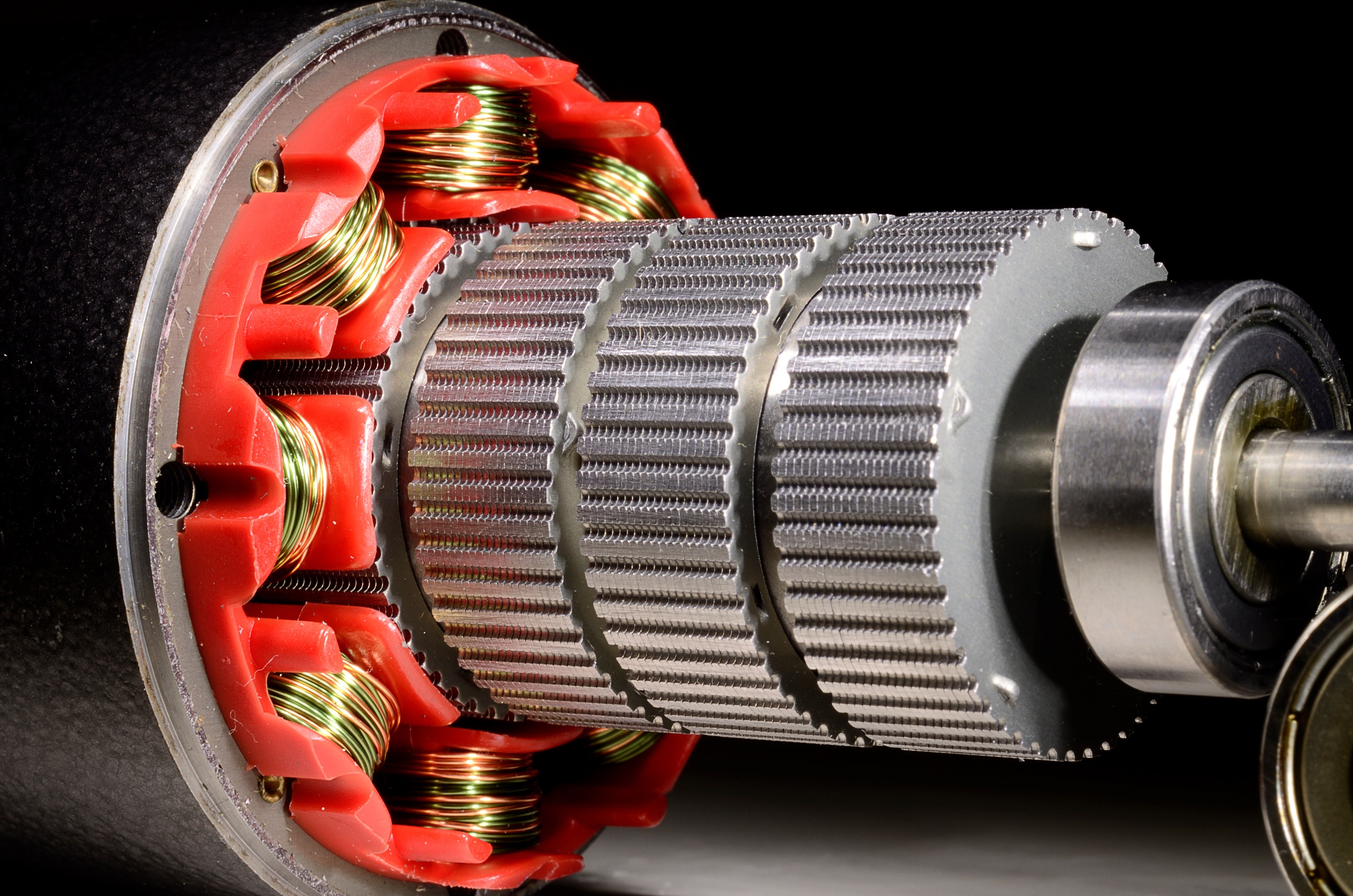
Operation of a brushless motor involves electricity delivered directly to immobile coils placed on the stator. Meanwhile, the rotor is a permanent magnet.
Higher efficiency and power
Brushless motors, with their unique design, offer increased efficiency and higher power. Eliminating mechanical resistance allows better application of the battery’s energy, which translates to more efficient operation. The power of brushless motors may be 20-30% higher than in the case of traditional motors with brushes.
Lower weight and smaller dimensions
Removal of carbon brushes and mechanical commutator enabled reduction of the motors’ size and weight. This translates to lighter and more compact power tools and increased comfort at work, especially in the case of prolonged use.
Fewer breakdowns
With no carbon brushes, a frequent source of breakdowns in traditional motors, the risk of damage is significantly lower, prolonging durability of power tools. Power tools with brushless motors require less maintenance and are more trouble-free in the long term.
Higher durability
Long-term loads may lead to quick wear and tear of traditional motors, but their impact is significantly lower in the case of brushless motors. With lowering of heat generation and elimination of sparks which may lead to overheating and damage, these power tools may be used for a much longer time, which is an excellent choice for professionals who use the tools intensively, as well as for ambitious amateurs.